Compartir:
Índice
En el entorno de la Industria 4.0, el mantenimiento industrial se está transformando en un mantenimiento industrial inteligente gracias a la integración de IA en el mantenimiento. En la era digital, predecir y prevenir averías aumenta la disponibilidad de los equipos y mejora la eficiencia operativa. Muchas empresas de mantenimiento predictivo ya incorporan IA y sensores inteligentes, lo que evidencia la creciente demanda de servicios de mantenimiento predictivo avanzados. Este artículo técnico pero accesible describe qué es el mantenimiento predictivo con IA, cómo funciona, sus beneficios y retos, comparándolo con el mantenimiento preventivo, y ofrece herramientas para elegir la estrategia adecuada.
La complejidad de los sistemas actuales hace fundamental la formación continua. En cursos de mantenimiento industrial 4.0, los profesionales aprenden a aplicar inteligencia artificial en mantenimiento; y en cursos de gestión de mantenimiento industrial se integran procesos y tecnología. Invertir en estos conocimientos estratégicos permite a las empresas adoptar un mantenimiento predictivo con IA que redunde en ahorro de costes y mayor competitividad
A través de estos cursos, aprenderás a implementar estrategias de mantenimiento preventivo, predictivo y proactivo, así como a utilizar tecnologías avanzadas como el IoT y la inteligencia artificial para optimizar la eficiencia operativa de tu empresa.
Además, si deseas especializarte en el área de mantenimiento industrial o necesitas asesoramiento personalizado, también ofrecemos servicios de consultoría personalizados, pregunta en el apartado de servicios de formación a medida para empresas.
1. ¿Qué es el mantenimiento predictivo?
El mantenimiento predictivo es una estrategia basada en el análisis de datos reales de los equipos para anticipar fallos antes de que ocurran. En lugar de trabajar por horarios fijos, se utilizan sensores y algoritmos de IA para monitorear indicadores críticos (vibraciones, temperatura, presión, desgaste, etc.) y detectar anomalías sutiles. De este modo se programa el mantenimiento justo cuando es necesario, extendiendo la vida útil de los activos y evitando paradas innecesarias. Las tecnologías 4.0 en mantenimiento (sensores IoT, redes industriales y sistemas de análisis en la nube) integran los datos operativos con algoritmos de aprendizaje automático que extraen información relevante. Por ejemplo, un sensor de vibración puede alertar si una máquina supera los umbrales normales, permitiendo intervenir antes de que falle.
1.1 Funcionamiento y arquitectura del sistema
Un sistema típico de mantenimiento predictivo incluye varios componentes integrados: recopilación de datos, almacenamiento, procesamiento y alerta. Primero, sensores inteligentes instalados en la maquinaria (vibración, ultrasonidos, termografía, análisis de aceite, corriente eléctrica, sonido, etc.) recogen señales en tiempo real. Esos datos se envían a plataformas de Big Data donde se transforman y analizan con técnicas de IA/ML. Los algoritmos de machine learning en mantenimiento industrial entrenan con datos históricos y condiciones normales para crear modelos predictivos. Cuando el modelo detecta un patrón inusual o un desvío del comportamiento esperado, genera una alerta. Finalmente, un sistema de visualización o un CMMS (Software de Gestión de Mantenimiento) recomienda acciones específicas para evitar la avería. Según AWS, este proceso permite “predecir el estado futuro del equipo y anticipar problemas antes de que surjan”, maximizando el tiempo de actividad y la fiabilidad de los activos.
1.2 Implementación práctica
Poner en marcha el mantenimiento predictivo con IA requiere planificar varios pasos clave. Primero se realiza una evaluación de activos críticos, identificando los equipos cuyo fallo es más costoso o peligroso. Luego, se instalan y calibran sensores adecuados (p.ej., vibración, temperatura, presión) conectados a plataformas de IoT. A continuación, se recopilan datos históricos y en tiempo real para entrenar los modelos de IA: a mayor volumen y calidad de datos, mejores predicciones. El desarrollo de modelos predictivos con algoritmos de aprendizaje automático (regresión, redes neuronales, random forest, etc.) es fundamental. Paralelamente, se capacita al personal de mantenimiento en estas nuevas herramientas, fomentando una cultura proactiva. Finalmente, se establecen rutinas de monitoreo y mejora continua, revisando periódicamente el rendimiento del sistema y ajustando modelos según la retroalimentación. Por ejemplo, una planta química redujo sus costos de mantenimiento en un 25% en el primer año tras seguir estos pasos de implementación.
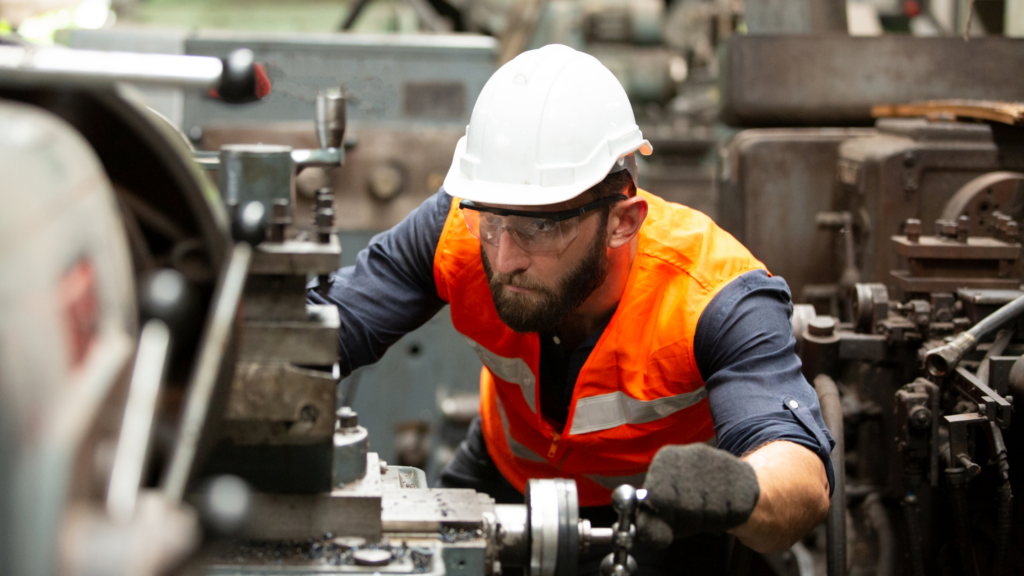
2. Beneficios del mantenimiento predictivo con IA
La adopción de mantenimiento predictivo con IA ofrece múltiples ventajas operativas y económicas:
- Reducción de tiempos de inactividad: Al predecir fallos con antelación, se evitan paradas no planificadas. Estudios señalan disminuciones del 15–30 % en interrupciones inesperadas al usar IA en mantenimiento.
- Ahorro de costos: Se optimizan los recursos al realizar tareas solo cuando son necesarias. Las empresas que aplican mantenimiento predictivo logran reducir 20–30 % sus costos operativos de mantenimiento.
- Mayor disponibilidad y productividad: La máquina pasa más tiempo operativa y se prolonga su vida útil. La optimización de mantenimiento industrial con IA aumenta la eficiencia operativa global y la productividad de la planta.
- Seguridad mejorada: Al anticipar fallos en equipos críticos (motores, bombas, estructuras móviles, etc.), se reducen accidentes laborales. La detección temprana de defectos protege al personal y al propio equipo.
- Planificación y uso eficiente de recursos: La IA sugiere cuándo asignar mano de obra y repuestos, minimizando costes de inventario y mejorando la gestión del almacén de repuestos. En resumen, la IA permite programar intervenciones precisas, evitando reparaciones costosas y prolongando la vida de los activos.
Estos beneficios se traducen en una ventaja competitiva clara. En industrias como la automotriz, energética y transporte, la IA en mantenimiento predictivo ya está mejorando la continuidad operativa y reduciendo costos (p.ej., aerolíneas aplican IA a sus flotas para mejorar la seguridad y eficiencia).
3. Tecnologías 4.0 en el mantenimiento inteligente
El mantenimiento industrial inteligente se sustenta en un ecosistema de tecnologías 4.0. Entre ellas destacan:
- Internet de las Cosas (IoT) y sensores inteligentes: Detectan variables clave (vibraciones, acústica, temperatura, corriente, análisis de aceite, etc.) y las transmiten en tiempo real. Por ejemplo, sensores inalámbricos de vibración y temperatura permiten monitorear maquinaria con mayor frecuencia y seguridad.
- Big Data y Cloud: Almacenan y procesan los grandes volúmenes de datos generados por los sensores. Plataformas en la nube facilitan el análisis masivo y escalable, esencial para alimentar los modelos de IA.
- Inteligencia Artificial y Machine Learning: Analizan los datos para identificar patrones ocultos. Gracias al machine learning en mantenimiento industrial, los sistemas aprenden continuamente de las condiciones operativas y mejoran sus predicciones con el tiempo. A diferencia de sistemas estáticos, los modelos basados en ML se auto ajustan con nuevos datos, aumentando su precisión y adaptándose a nuevas circunstancias.
- Analítica avanzada: Tecnologías de visualización y soporte a la toma de decisiones traducen la información compleja en cuadros de mando intuitivos. Esto facilita a los técnicos y gerentes entender la salud de los activos y priorizar acciones.
- Robótica y visión artificial: En ciertos casos, drones o cámaras termográficas inspeccionan áreas peligrosas de forma remota, completando la monitorización con IA. Estas tecnologías amplían la cobertura del mantenimiento predictivo a entornos difíciles.
La confluencia de estas tecnologías permite la optimización digital de activos industriales, donde los equipos “hablan” y sugieren cuándo necesitan atención. En suma, el mantenimiento inteligente basado en IA cambia el paradigma de “reparar tras la rotura” a prevenir problemas antes de que ocurran.
4. Mantenimiento predictivo frente a preventivo
Aunque ambos buscan reducir fallos, mantener prediciendo y mantener previniendo tienen enfoques distintos. El mantenimiento preventivo se basa en calendarios fijos: tareas programadas por tiempo o uso (p.ej. cambio de aceite cada 6 meses). Es relativamente fácil de planificar y reduce muchas averías, pero puede generar tareas innecesarias si el equipo está en buen estado, lo que conlleva costes por intervenciones prematuras.
En cambio, el mantenimiento predictivo (con IA) se basa en el estado real del equipo: solo se actúa cuando los datos indican deterioro. Así se evitan paradas prematuras y se minimiza el downtime no planificado. Como señalan expertos, “el mantenimiento predictivo se programa según las condiciones de los activos en tiempo real” a diferencia del preventivo, que se programa periódicamente. Una fuente indica que el predictivo puede ahorrar entre 25 % y 30 % más que el correctivo, comparado con 12–18 % del preventivo.
En resumen, la principal diferencia es la base de decisión: el predictivo utiliza el monitoreo continuo del estado del activo, mientras el preventivo lo hace en función de intervalos predefinidos. En la práctica:
- Ventajas del predictivo: Menos mantenimiento innecesario, menor riesgo de fallos inesperados, mayor eficiencia de recursos.
- Desventajas del predictivo: Requiere inversión inicial en sensores, software y capacitación, y tiempo para implementar correctamente.
- Ventajas del preventivo: Simplicidad de implementación, menor inversión inicial, disminuye incidentes en equipos no monitoreados.
- Desventajas del preventivo: Puede sobremanipular equipos, generando costes extra, y no garantiza detección de fallos que ocurren entre intervenciones programadas.
A nivel estratégico, el predictivo es más apropiado cuando la criticidad o el costo de parada son altos, mientras el preventivo es útil en entornos menos digitalizados o con recursos más limitados.
5. Comparativa de tipos de mantenimiento
Además de predictivo y preventivo, existen otros enfoques (correctivo, reactivo, proactivo). A continuación se presenta una tabla comparativa según criterios clave:
Criterio | Correctivo (Reactivo) | Preventivo | Predictivo | Proactivo |
---|---|---|---|---|
Coste inicial | Muy bajo (solo reparación tras falla) | Bajo (rutinas programadas, herramientas básicas) | Alto (inversión en sensores, software y analítica) | Alto (analiza causas raíz; requiere herramientas avanzadas) |
Disponibilidad | Muy baja (paradas inesperadas) | Media (paradas planificadas) | Alta (se minimizan paros imprevistos) | Muy alta (equipos optimizados, fallos prácticamente evitados) |
Riesgo operativo | Muy alto (solo reacciona al fallo) | Medio (reducción de fallos comunes) | Bajo (adelanta las averías antes de daño) | Mínimo (elimina causas raíz de fallos) |
Tecnología necesaria | Mínima (no requiere monitorización) | Baja (planificación simple, inspecciones rutinarias) | Alta (sensores, IoT, análisis de datos, IA) | Muy alta (análisis de confiabilidad, RCM, mejoras de diseño) |
Tabla 1. Comparativa de tipos de mantenimiento según coste, disponibilidad, riesgo y tecnología.
Esta tabla muestra que el mantenimiento correctivo (reparar tras falla) es simple pero arriesgado. El preventivo mejora la fiabilidad con rutinas, pero sin datos reales del estado. El predictivo aprovecha la analítica para anticipar, requiriendo inversión tecnológica. El proactivo va más allá: se enfoca en eliminar las causas raíces (rediseñando equipos o procesos) para evitar fallos desde su origen.
5. ¿Cómo elegir el mantenimiento adecuado?
No existe una única solución para todos los casos. La decisión depende de variables como el tipo de maquinaria, el nivel de digitalización de la planta, los recursos disponibles y la criticidad de la operación. La siguiente tabla de autoevaluación ayuda a orientar la elección:
Variable | Escenario o Contexto | Mantenimiento sugerido |
---|---|---|
Tipo de maquinaria | Equipos simples, no críticos (herrería, máquinas auxiliares) | Preventivo o correctivo |
Equipos complejos o de alta exigencia (líneas de producción críticas) | Predictivo o proactivo | |
Nivel de digitalización | Bajo (sin sensores o sistemas avanzados) | Preventivo (tecnologías sencillas) |
Alto (IoT, redes industriales y sistemas de monitoreo) | Predictivo (aprovechar datos disponibles) | |
Recursos disponibles | Limitados (personal y presupuesto estrechos) | Correctivo/Preventivo (baja inversión inicial) |
Abundantes (capacidad de inversión en tecnología y formación) | Predictivo o proactivo (retorno a largo plazo) | |
Criticidad operativa | Baja (paro tolerable, bajo impacto) | Preventivo (enfoque conservador) |
Alta (parada cara, equipos esenciales) | Predictivo o proactivo (máxima fiabilidad) |
Tabla 2. Guía de autoevaluación: qué tipo de mantenimiento conviene según las características del equipo y la operación.
Esta guía sugiere, por ejemplo, que máquinas no críticas y baja digitalización pueden mantenerse con métodos preventivo o incluso reactivo, mientras que en entornos muy digitalizados y con activos críticos es rentable apostar por el mantenimiento predictivo apoyado en IA e IoT. En cualquier caso, es común combinar estrategias: por ejemplo, aplicar mantenimiento preventivo en equipos secundarios y concentrar la analítica avanzada (predictivo/proactivo) en aquellos de mayor riesgo.
El éxito del mantenimiento predictivo con IA depende de la capacitación continua del personal y su adaptación a nuevas tecnologías.
6. Implementación y desafíos
6.1 Pasos de implementación
Para un mantenimiento predictivo con IA exitoso, conviene seguir una hoja de ruta clara (como la descrita en la Tabla 1). Resumidamente:
- Evaluación inicial: Identificar activos críticos y objetivos (reducción de paradas, costos, etc.).
- Instalación de sensores: Colocar dispositivos IoT adecuados en puntos clave (vibración, temperatura, ultrasonidos, etc.)
- Integración de sistemas: Conectar los sensores a una plataforma de análisis en la nube o local.
- Desarrollo de modelos predictivos: Recopilar datos históricos y en tiempo real para entrenar algoritmos de IA que detecten patrones de fallo.
- Formación del personal: Capacitar a técnicos en nuevas tecnologías, análisis de datos y software asociado.
- Monitoreo continuo y mejora: Revisar regularmente los resultados, ajustar umbrales y modelos, y realimentar el sistema con nueva información.
Siguiendo estos pasos, las organizaciones transforman sus rutinas y pasan de un modelo reactivo a uno predictivo. Según datos de la industria, las empresas que adoptan IA en mantenimiento ven mejoras del 10–20 % en productividad y reducen hasta un 20 % los costes asociados.
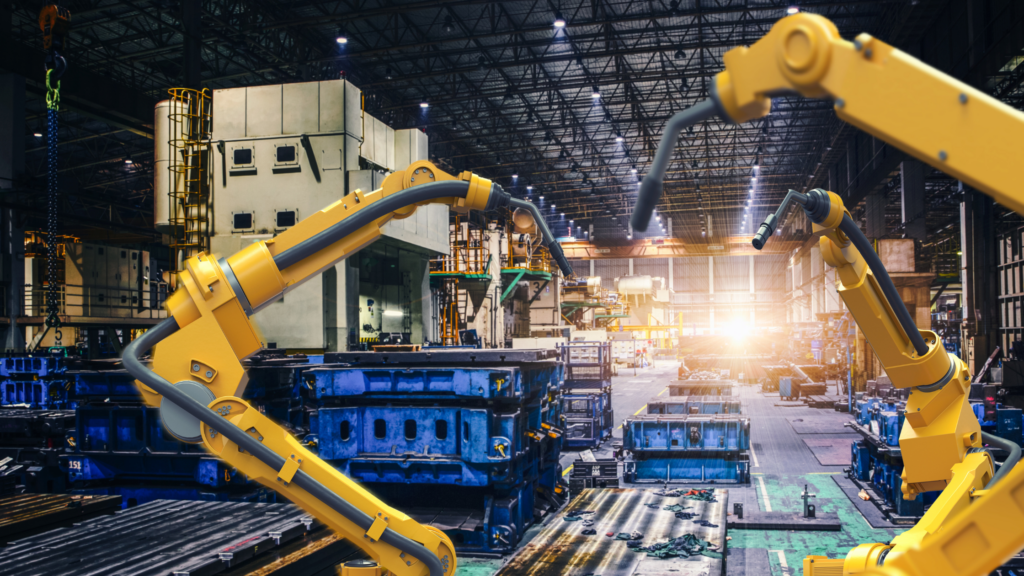
6.2 Principales desafíos
Aunque prometedor, el mantenimiento predictivo con IA implica varios retos prácticos:
- Alta inversión inicial: Los sensores avanzados, el software analítico y la infraestructura de datos requieren desembolsos importantes. Es crucial evaluar el retorno a largo plazo y considerar implementaciones escalonadas.
- Gestión de grandes volúmenes de datos: Capturar, almacenar y procesar datos de múltiples sensores exige robusta infraestructura (servidores, ancho de banda, nube) y planificación de Big Data.
- Calidad de los datos: Los modelos de IA solo son tan buenos como los datos que reciben. Ruido, sensores defectuosos o datos incompletos pueden invalidar predicciones. Se necesita limpieza y validación constante de los datos.
- Integración con sistemas existentes: Conectar nuevas tecnologías con la planta (redes OT/IT, CMMS, SCADA) puede ser complejo. Se recomienda usar protocolos estándar y trabajar con especialistas en integración.
- Resistencia al cambio: Pasar de mantenimiento basado en calendario a uno basado en datos requiere un cambio cultural. El personal debe entender y confiar en las nuevas herramientas. La formación y la comunicación efectiva sobre beneficios son clave.
- Seguridad informática: Las conexiones IoT abren puertas a ciberataques. Es indispensable asegurar las comunicaciones y las plataformas de mantenimiento para proteger la operación.
- Capacitación de talento: Se precisa personal cualificado en análisis de datos e IA. Esto significa invertir en entrenamiento o en alianzas con proveedores especializados.
Abordar estos desafíos es fundamental para obtener los beneficios esperados. Con la estrategia adecuada, los resultados suelen incluir menos interrupciones, operaciones más eficientes y una transformación digital duradera.
7. Formación continua y valor estratégico
En un escenario tan dinámico, la formación continua es esencial. Adquirir competencias en mantenimiento 4.0 e IA no solo mejora la gestión diaria, sino que se convierte en una ventaja competitiva estratégica. Por ello, se invita a los profesionales y responsables técnicos a profundizar sus conocimientos mediante los cursos ofrecidos: “Mantenimiento Industrial 4.0 con IA”, “Optimización Digital de Activos Industriales” y “Gestión de Mantenimiento Industrial”. Estos programas abordan desde la implementación de tecnologías avanzadas hasta el análisis de datos en mantenimiento. Invertir en capacitación garantiza que el personal esté preparado para liderar la digitalización del mantenimiento, adaptarse a los retos futuros y explotar al máximo las oportunidades de la Industria 4.0.
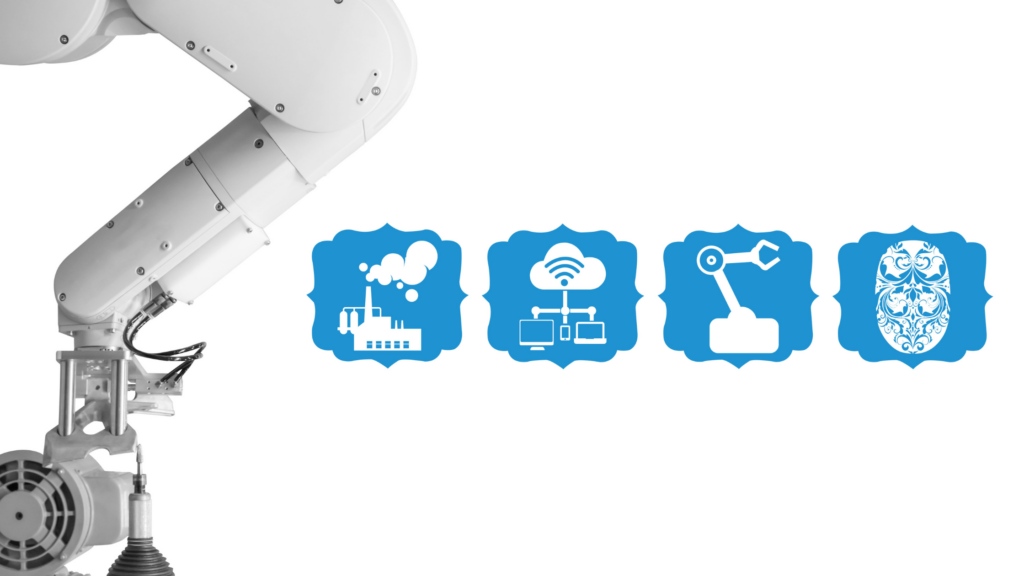
8. Conclusión
El mantenimiento predictivo con IA representa un cambio de paradigma en la gestión de activos industriales. Al integrar inteligencia artificial, machine learning e IoT en las estrategias de mantenimiento, las empresas avanzan hacia un modelo mucho más eficiente y competitivo. Aunque la adopción requiere inversiones y esfuerzo, los beneficios –menores costes operativos, mayor disponibilidad, extensión de la vida útil de equipos y mejora en la seguridad– justifican con creces la apuesta tecnológica.
La Industria 4.0 está redefiniendo el mantenimiento, y aquellos que aprovechen estas innovaciones podrán prevenir fallos en lugar de reaccionar ante ellos. En el contexto actual, los datos son un activo clave. Por tanto, fomentar una cultura de monitoreo continuo, analítica avanzada y mejora continua es esencial. En última instancia, la transformación digital del mantenimiento industrial no solo optimiza operaciones, sino que impulsa la sostenibilidad y la rentabilidad del negocio. Prepararse con formación especializada y adoptar herramientas predictivas de IA es el camino hacia una gestión de mantenimiento más estratégica, inteligente y proactiva.
Descubre nuestros cursos relacionados
Preguntas Frecuentes (FAQs)
La IA permite detectar fallos antes de que ocurran, reduciendo tiempos de inactividad y evitando reparaciones costosas.
El mantenimiento predictivo utiliza datos y análisis en tiempo real para anticiparse a problemas, mientras que el preventivo sigue un calendario regular sin necesidad de datos en tiempo real.
Prácticamente cualquier maquinaria industrial, desde motores y generadores hasta sistemas complejos en fábricas, se beneficia de la implementación de IA.
La IA en la Industria 4.0 mejora la eficiencia, optimiza el uso de recursos, y ayuda a las empresas a mantenerse competitivas mediante una gestión proactiva de los activos.
Compartir: